Are disjointed control of work processes leaving you open to risk?
Dependable Lock Out Tag Out
Your Key to Workplace Safety
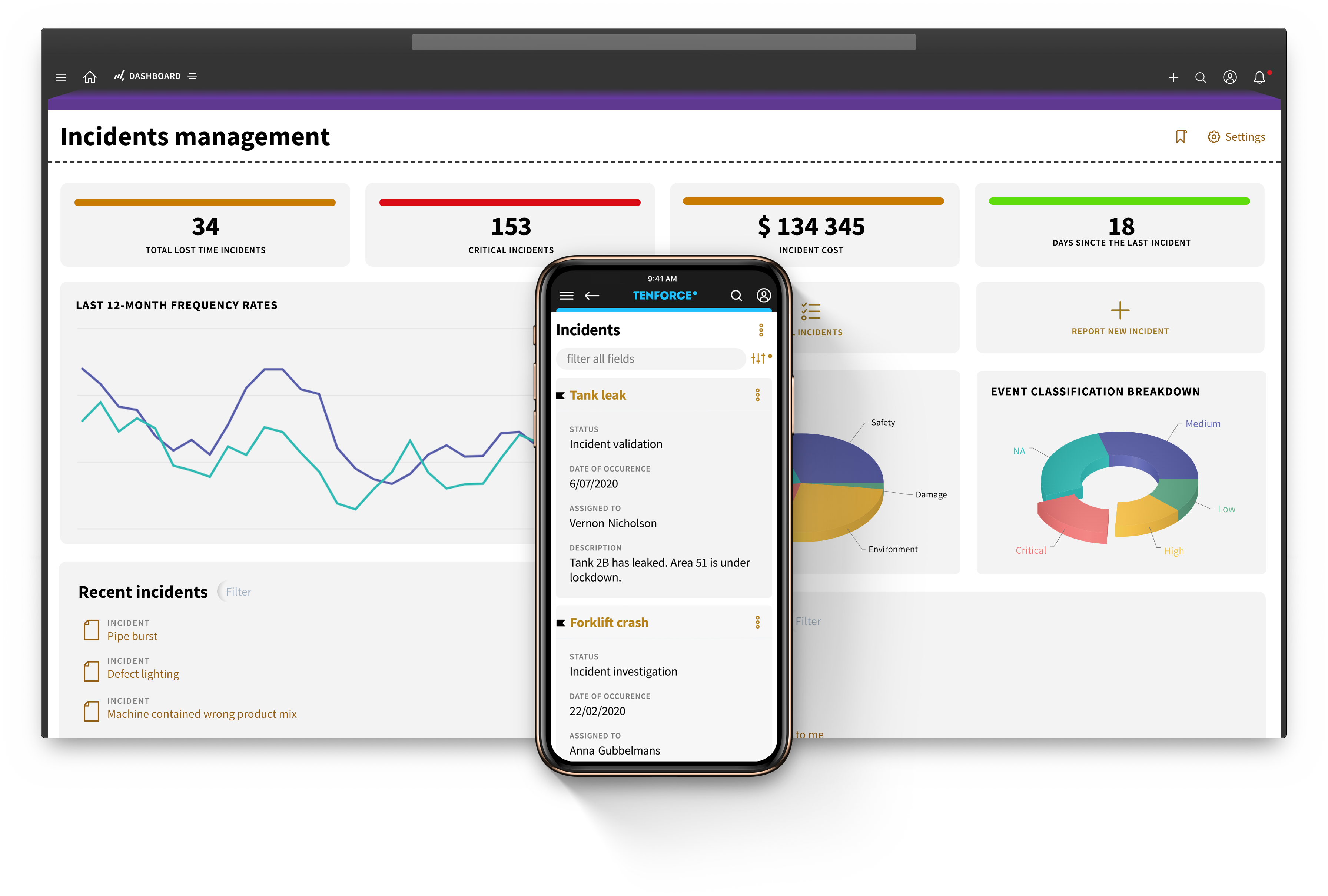
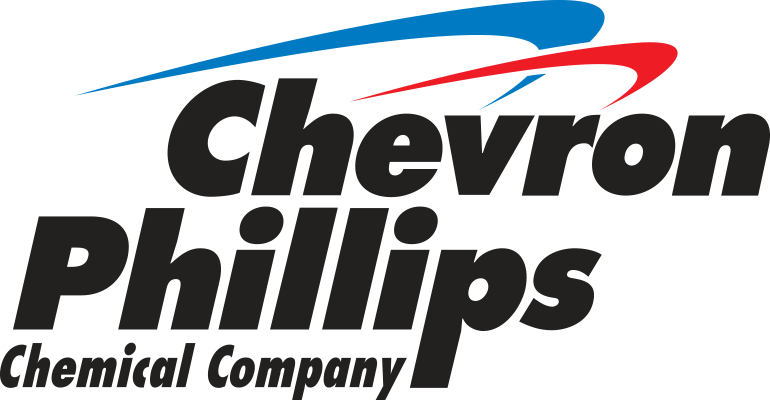
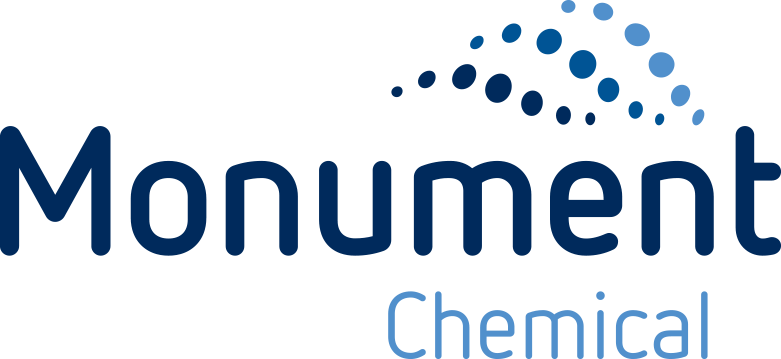
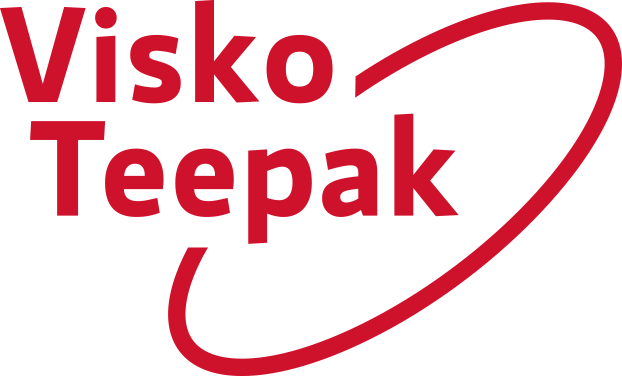
Uncompromising Safety, Every Lockout Tagout
1
LOTO Procedure Creation and Lockout/Tagout Application
- Create LOTO procedures for specific equipment or machinery
- Define the energy sources, isolation points, and steps required for safe shutdown
- Ensure procedures comply with safety standards and regulations
- Authorized personnel initiate the LOTO process when performing maintenance or servicing
- Energy sources isolated and locks and tags applied per the approved procedure
2
Permit to Work Integration
- Notify all affected employees about the LOTO procedures
- Integrate LOTO with the Permit to Work (PTW) system
- Ensure PTW includes information about ongoing LOTO activities
3
Verification and Testing
- Verify that energy sources are effectively isolated
- Test equipment to ensure it is non-operational before work begins
4
Verification and Testing
- Maintenance or servicing work can commence safely
- Continuous monitoring to prevent unauthorized removal of locks/tags
- Report any deviations from the LOTO procedure
- Investigate and take corrective actions promptly
5
LOTO Removal and Equipment Restoration
- After work completion, authorized personnel remove locks/tags
- Ensure equipment is restored to operational status safely
Secure Your Peace of Mind
Safety Assurance
Ensure precision and accountability in lockout/tagout procedures by creating a clear record of who performed them, when, and when they can be lifted. This meticulous approach minimizes the risk of errors and omissions, boosting safety protocols.
Streamlined, Up-to-Date Processes
Replace manual paperwork with electronic records to simplify the entire lockout/tagout procedure. This not only reduces administration but also allows for swift updates when equipment or processes change, keeping procedures up to date and efficient.
Cost-Efficiency and Savings
Streamline lockout/tagout processes to minimize downtime, leading to significant cost savings. And steer clear of potential fines and legal troubles tied to safety regulation non-compliance
Control and Compliance
Enhance security and prevent unauthorized interference by implementing role-based access control. Plus, automated record-keeping will also simplify compliance with regulations.
Insightful Reporting
Collect and analyze lockout/tagout data to identify trends and areas for improvement. Generate quick and easy reports for internal audits, regulatory compliance, and incident investigations.
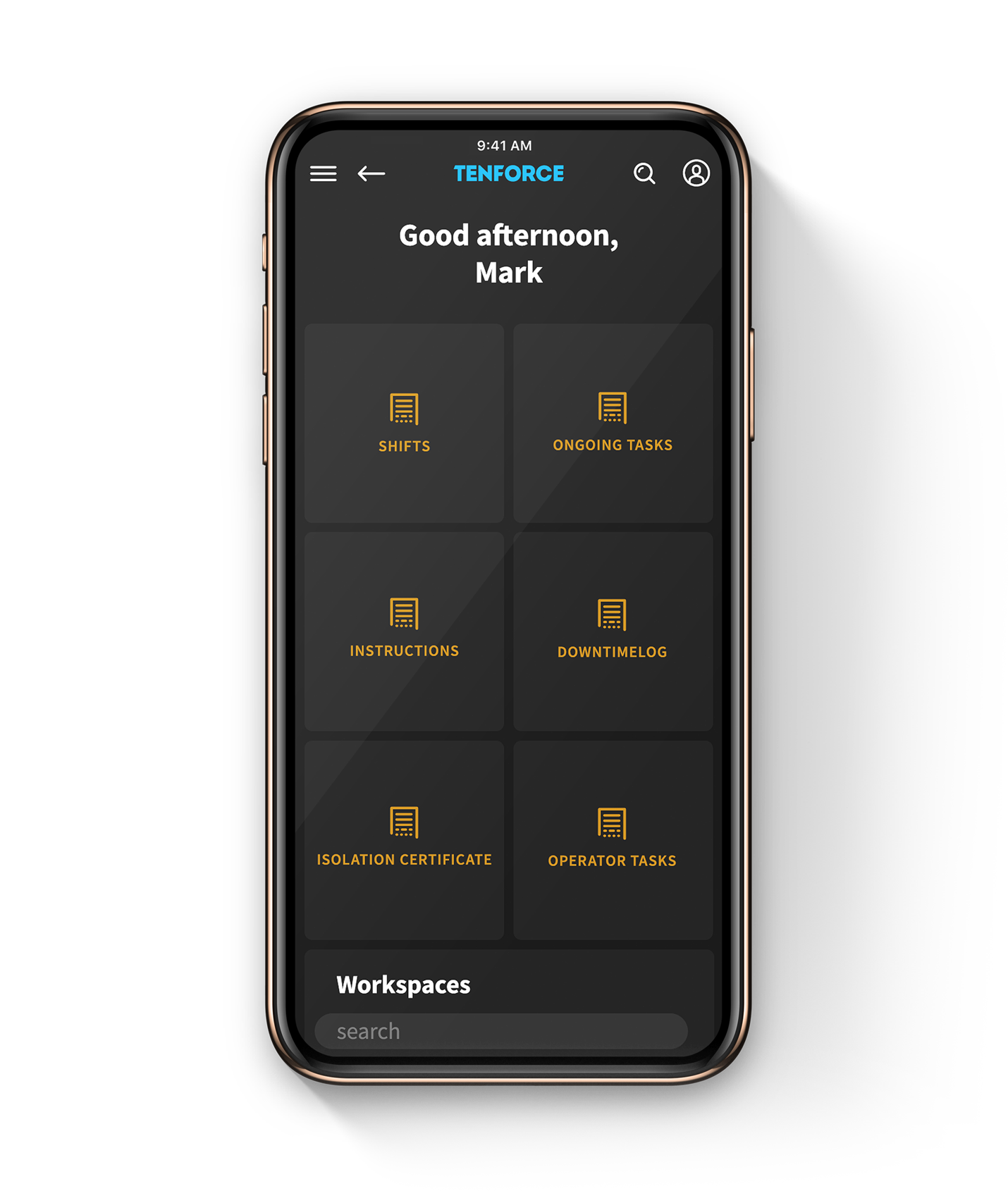
40%
decrease in incidents related to machinery startups during maintenance or servicing
20%
faster machinery shutdown and startup time, ensuring minimal operational downtime
Seamlessly integrate with other TenForce modules to unify your EHSQ processes
Audits & Inspections
Incident Management
LoTo
Permit to Work
Management of Change
Shift Management
Risk Management
Competence management
Quality management
Contractor Management
SAFETY DATASHEETS
MECHANICAL INTEGRITY
Document control
Complaint Handling
Environmental Management
CAPA
Environmental reporting
Compliance calendar
Dive deeper into this topic
3 Reasons Centralizing Your Control of Work Processes Pays Off
In the last decade, we’ve seen promising improvements in safety performance, largely thanks to the adoption of EHS technology. Total Recordable Incident Rates (TRIR) are down, which is encouraging. But, there’s a but. Fatal incidents actually rose from 2011 to 2021.
This tells us there’s more work to do. Traditional safety practices like data collection and audits are key for compliance, but they don’t go far enough in preventing serious incidents.…
9 Common Lockout/Tagout Mistakes (+ Practical Tips to Prevent Them)
Lockout/Tagout (LOTO) procedures – they’re essential for protecting your workers from hazardous energy sources. By isolating energy sources and attaching a LOTO device to indicate that the equipment should not be used, you prevent accidental startup or the release of stored energy during maintenance.
What happens when procedures aren’t followed?
Here’s an example – the maintenance of a complex hydraulic press. In a rush to minimize downtime, the maintenance team bypasses key steps in the LOTO procedure.…
Your peers trust us
Our customers rely on TenForce to foster a proactive safety culture and drive continuous process improvement. The outcome? Increased team efficiency, reduced administrative burden, and significant cost savings due to fewer fines and incident-related downtime.
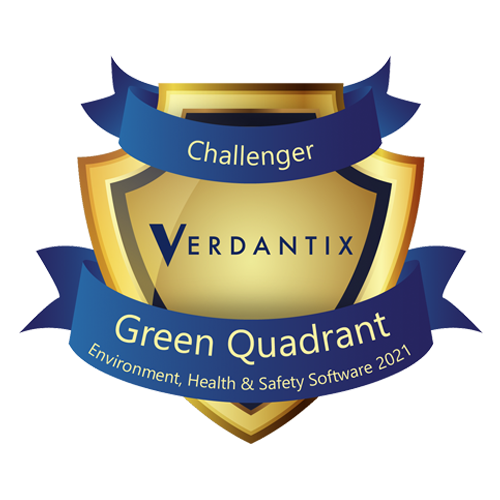
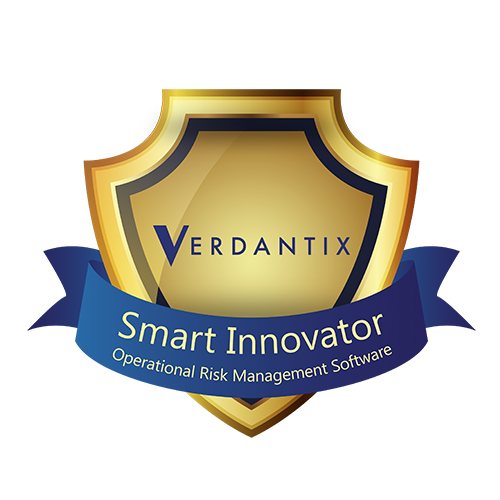
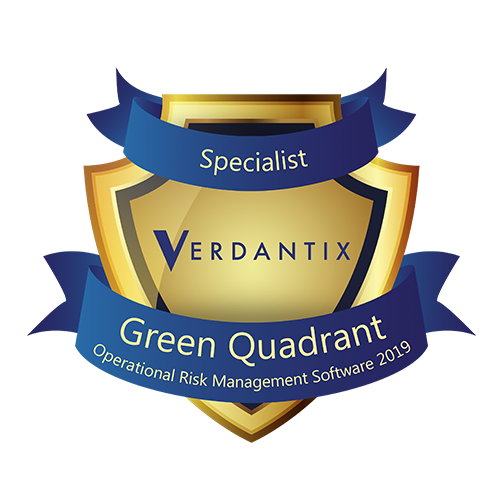
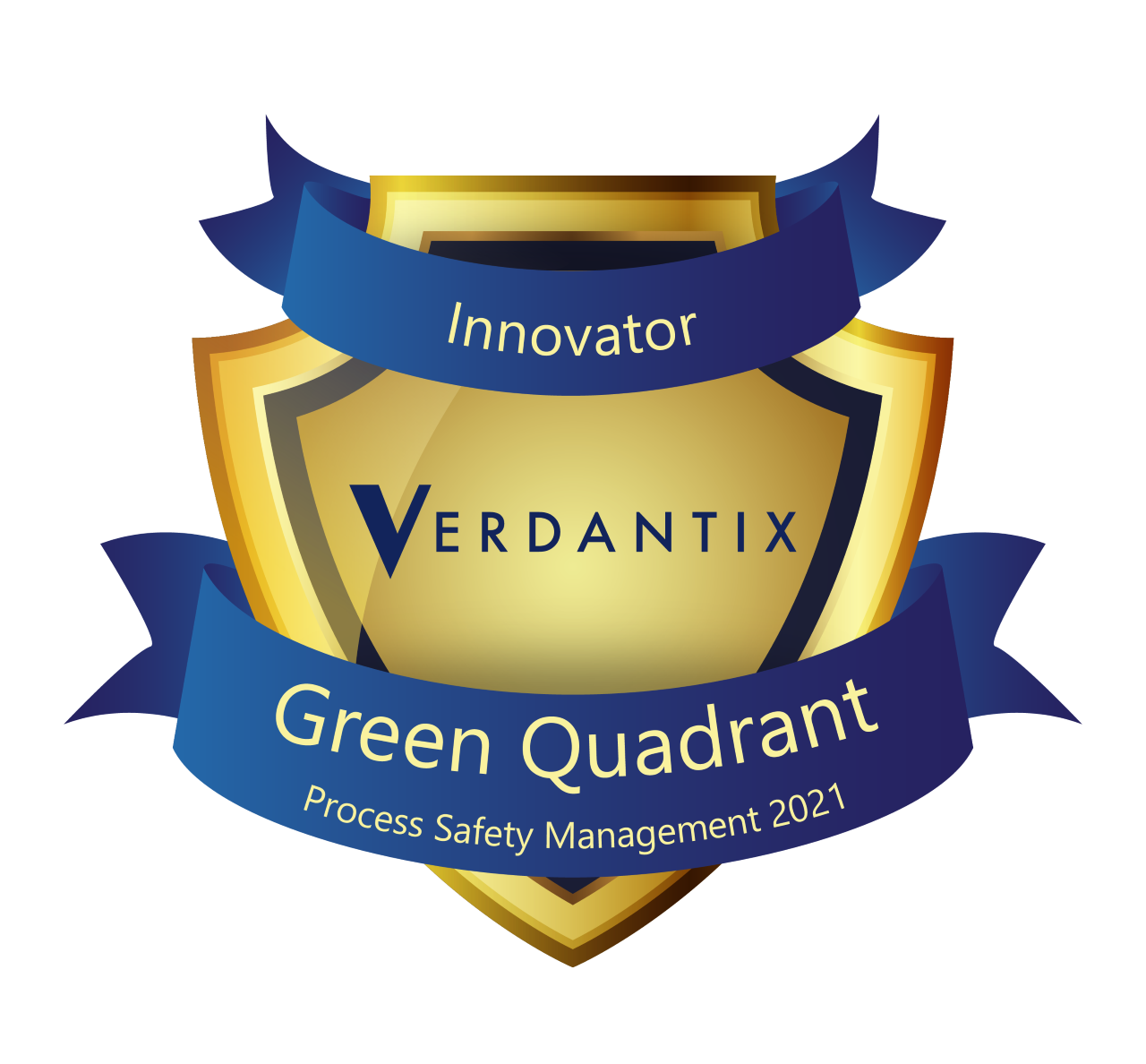
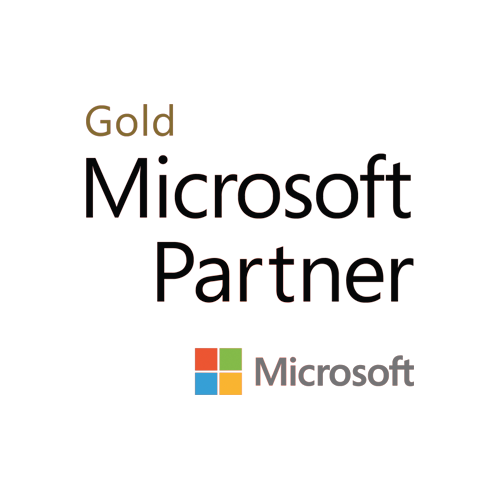
Book a demo
Curious to see how TenForce can make your workday easier? Book a demo, and we’ll show you what our EHSQ platform can do! One of our in-house experts will guide you through the ins and outs, showing you exactly how TenForce can tackle your challenges, whether it’s managing safety, streamlining compliance, or keeping quality in check.
So, choose a time that works for you, and let’s explore how TenForce fits into your day-to-day.
Ask us questions. Get clear answers. Share the recording with your colleagues.