Is your asset inventory and maintenance schedule in a muddle?
End-to-End Mechanical Integrity
Ensuring Equipment Excellence Every Step of the Way
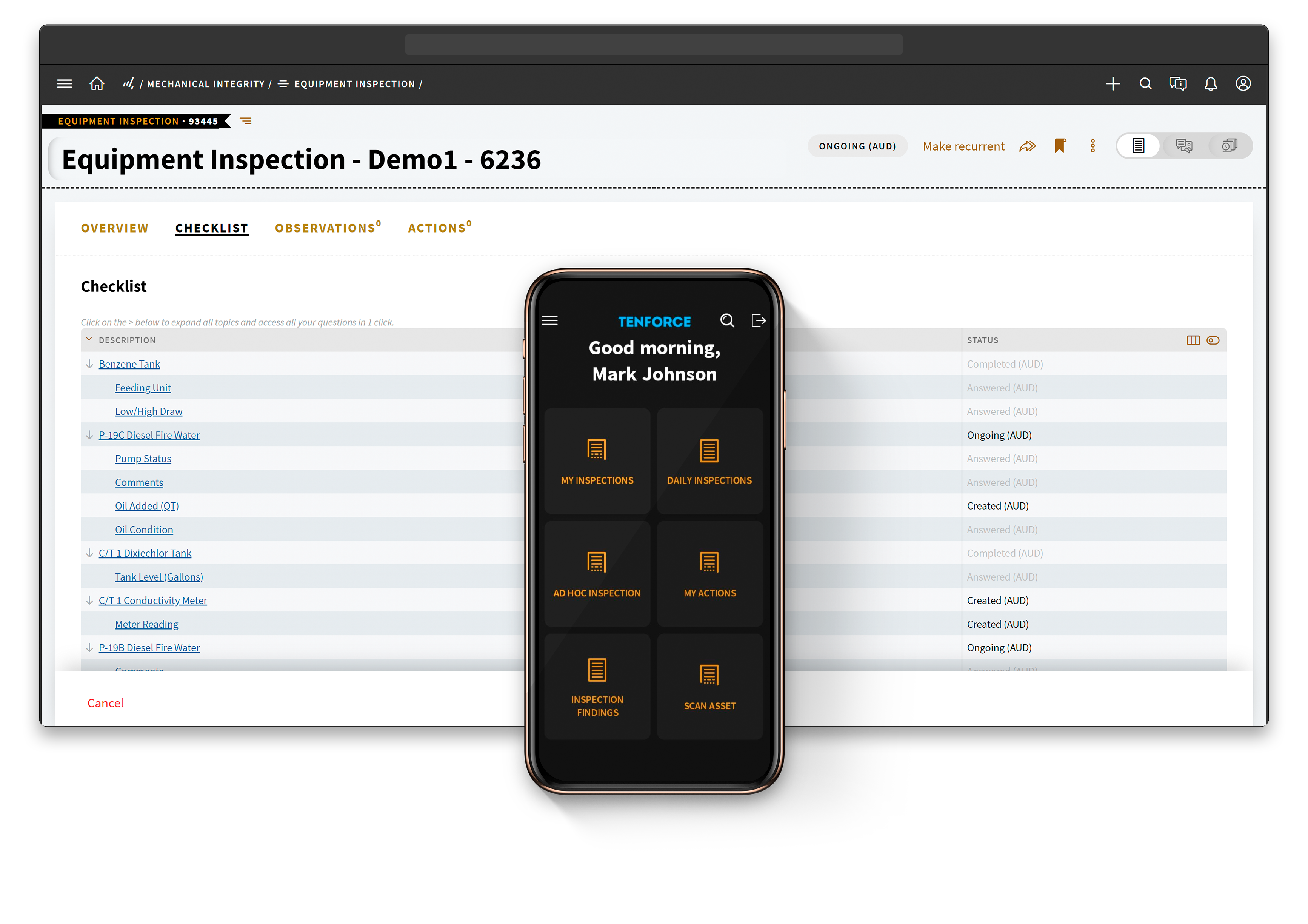
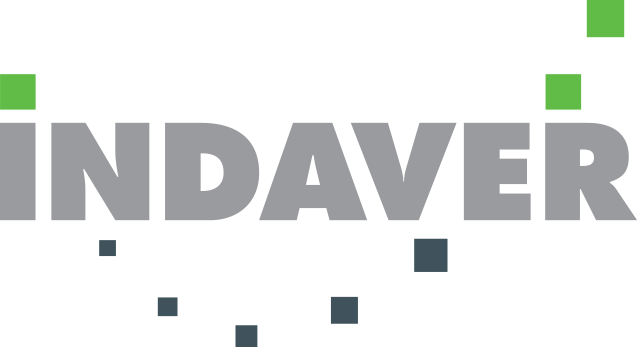
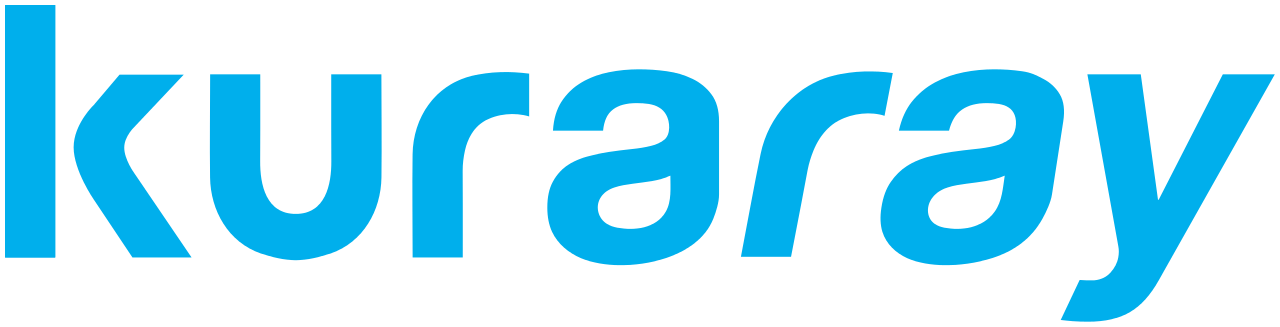
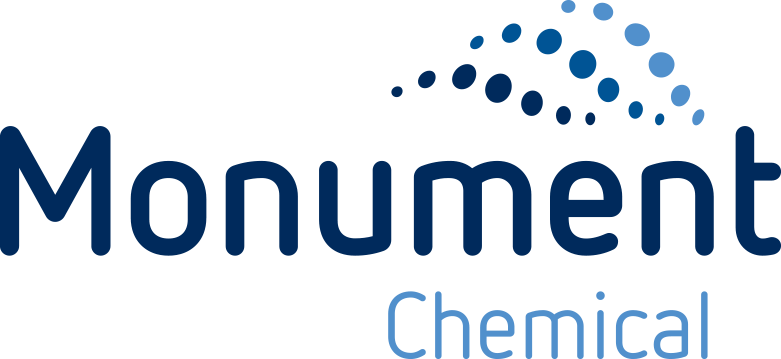
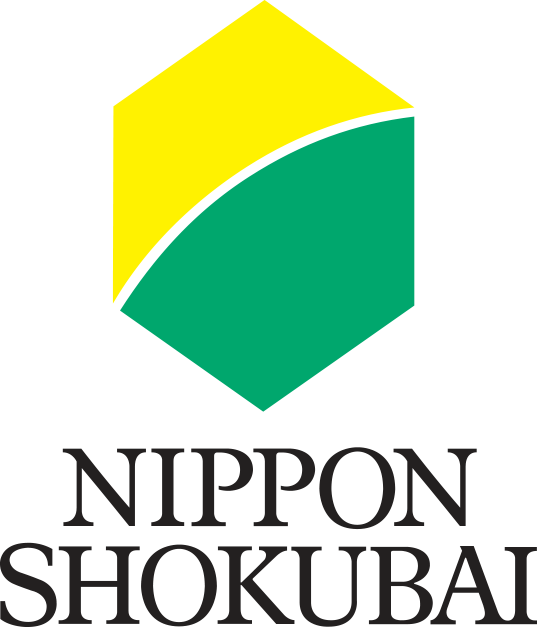
Closely Monitor the Complete Lifecycle of your Equipment
1
Maintenance Scheduling
Plan, prepare, execute, and follow up inspections. Identify and assign tasks and track their completion using escalating email notifications and dashboards that show completed, pending, and overdue tasks.
2
Asset Lifecycle Management
Maintain full asset lifecycle visibility, with viewable maintenance and inspection history. Ensure safety and technical oversight from commissioning through installation, maintenance, repair, and retirement or replacement of equipment.
3
Centralized Asset Inventory
Use web-based inspection forms and checklists to record consistent plant-wide inspection data and equipment-specific details, including location, part numbers, manuals, SOPs, and instrumentation diagrams.
4
Collect and Analyze Data
Analyze real-time data for quick defect detection, anomaly identification, and predictive maintenance prioritization. Keep a comprehensive asset history, including outages, malfunction analysis, and end-of-life decisions.
Maximize Uptime, Minimize Risk, Elevate Performance
Extend Asset Lifespan
Boost equipment longevity, minimize defects, reduce downtime, and enhance safety proactively. Prioritize asset maintenance based on risk factors such as criticality, safety implications, and compliance.
Automate Maintenance
Replace manual processes with automated maintenance and inspection scheduling. Record results and track corrective actions to completion for up-to-date, efficient operations.
Quality Assurance
Ensure equipment is used correctly and repaired with the appropriate parts and materials. Embed manufacturer specs and instructions into the testing, inspection, and maintenance process, guaranteeing top quality products.
Ensure Compliance
Simplify compliance with controlled processes and full traceability for the complete life cycle of your equipment. Automate safety checks and alerts, improving legal and best-practice compliance while reducing risks and maximizing safety.
Remote, Mobile and Offline Access
Stay connected with remote, offline functionality. Access forms and checklists from anywhere, even in no-connectivity areas, for on-site inspections and data entry.
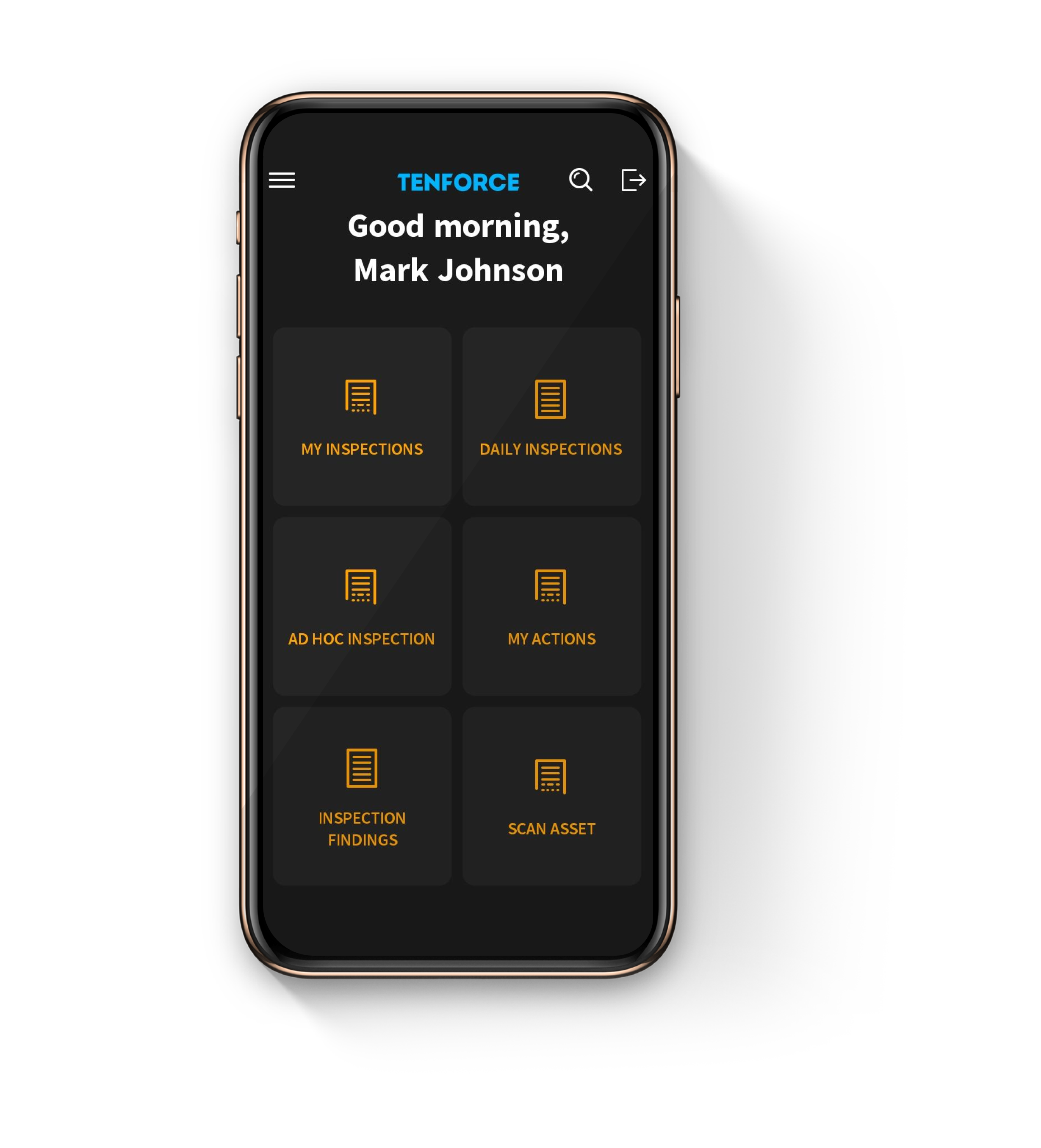
Improve equipment reliability by up to
50%
Reduce energy consumption by up to
15%
Seamlessly integrate with other TenForce modules to unify your EHSQ processes
Audits & Inspections
Incident Management
LoTo
Permit to Work
Management of Change
Shift Management
Risk Management
Competence management
Quality management
Contractor Management
SAFETY DATASHEETS
MECHANICAL INTEGRITY
Document control
Complaint Handling
Environmental Management
CAPA
Environmental reporting
Compliance calendar
Dive deeper into this topic
Put ‘P’ for ‘Prevention’ at the Top of the Alphabet with Mechanical Integrity
Mechanical Integrity (MI) is based on managing equipment and assets within your business, from installation through their entire lifecycle and eventual obsolescence. MI is a vital, if not the biggest, part of incident and injury prevention, and critical to Process Safety Management. The safety and well-being of employees depend on the quality and reliability of the equipment they work with, so it is vital that everything, even the smallest maintenance task, gets tracked.…
Bridging the Gap: How EHSQ Software De-escalates Tension Between Maintenance and Safety
When it comes to workplace friction, tensions between maintenance and safety can run high. Ask any maintenance worker for their top workplace complaint and it’s likely to involve the pressure of meeting strict deadlines; a problem often made worse by interruptions from the SHEQ (Safety, Health, Environmental, and Quality) manager about how to complete procedures safely.
Of course, failing to correctly follow maintenance procedures can lead to serious consequences. So, it’s no surprise that SHEQ managers monitor maintenance activities so closely.…
Your peers trust us
Our customers rely on TenForce to foster a proactive safety culture and drive continuous process improvement. The outcome? Increased team efficiency, reduced administrative burden, and significant cost savings due to fewer fines and incident-related downtime.
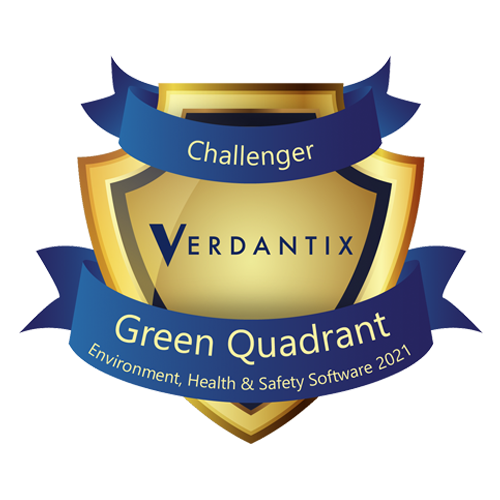
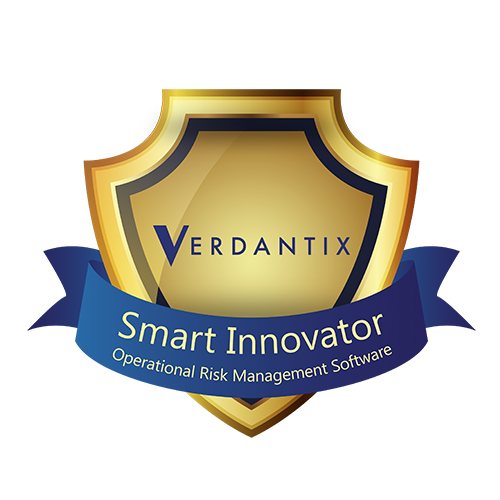
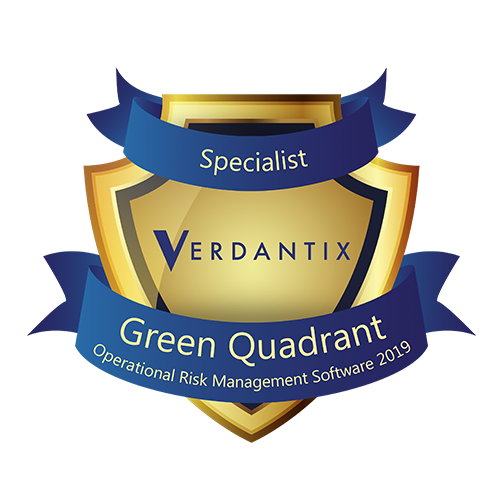
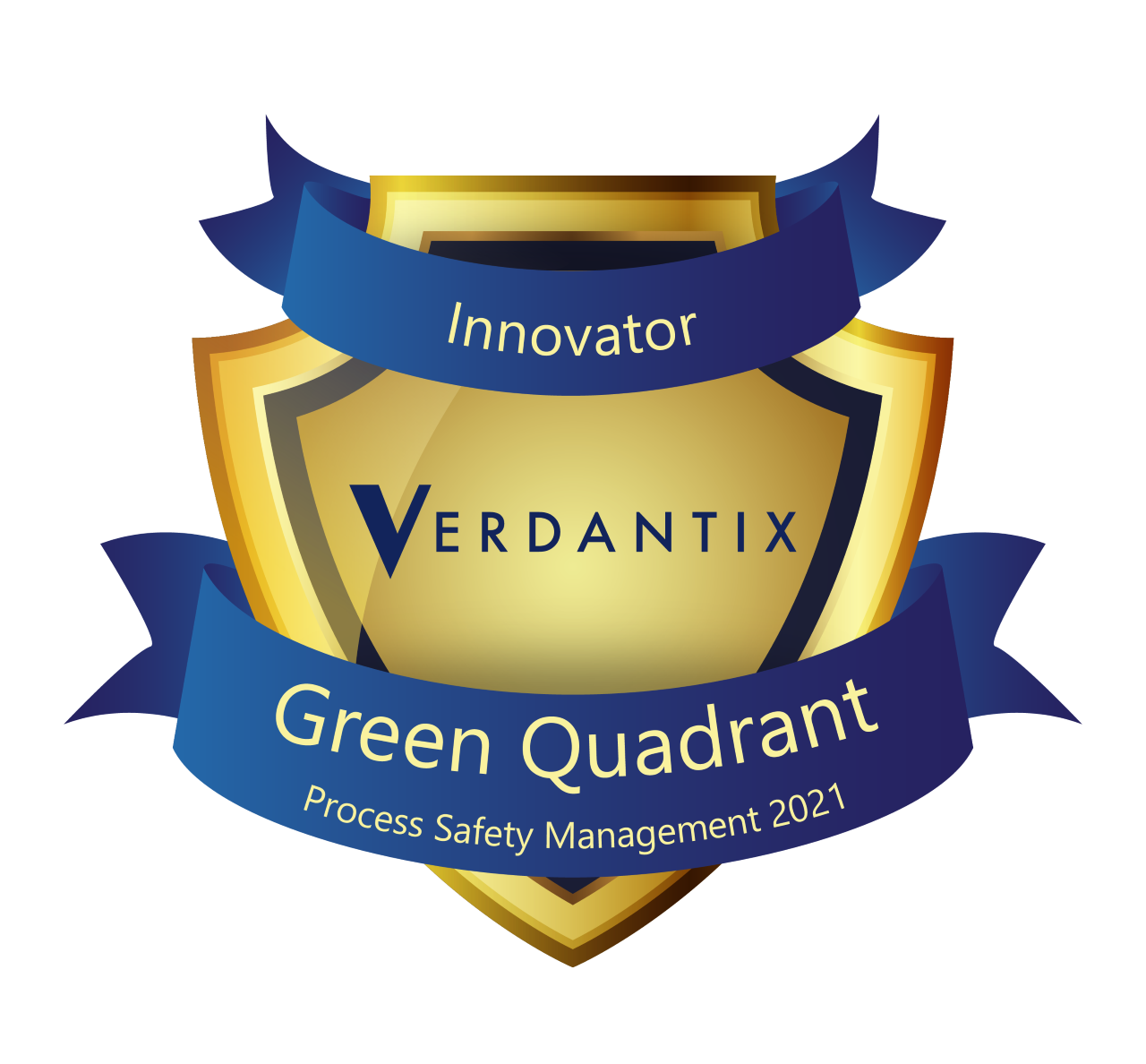
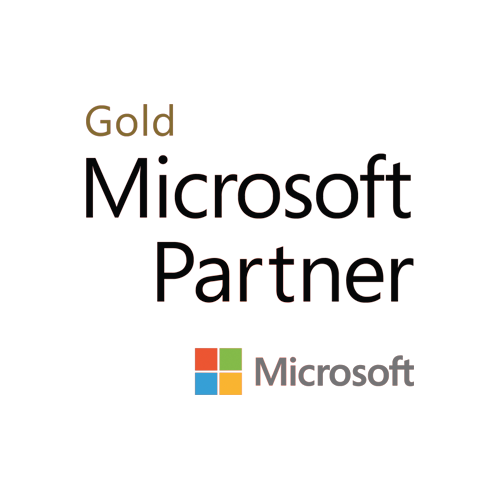
Book a demo
Curious to see how TenForce can make your workday easier? Book a demo, and we’ll show you what our EHSQ platform can do! One of our in-house experts will guide you through the ins and outs, showing you exactly how TenForce can tackle your challenges, whether it’s managing safety, streamlining compliance, or keeping quality in check.
So, choose a time that works for you, and let’s explore how TenForce fits into your day-to-day.
Ask us questions. Get clear answers. Share the recording with your colleagues.