Corrective and Preventive Action Management Software
Effectively manage CAPA across your organization.Proactively drive EHSQ compliance.
Watch demoChoose a complete software solution that meets the unique needs of your organization. Track, manage, and analyze your EHSQ non-conformities. Stay accountable and compliant.
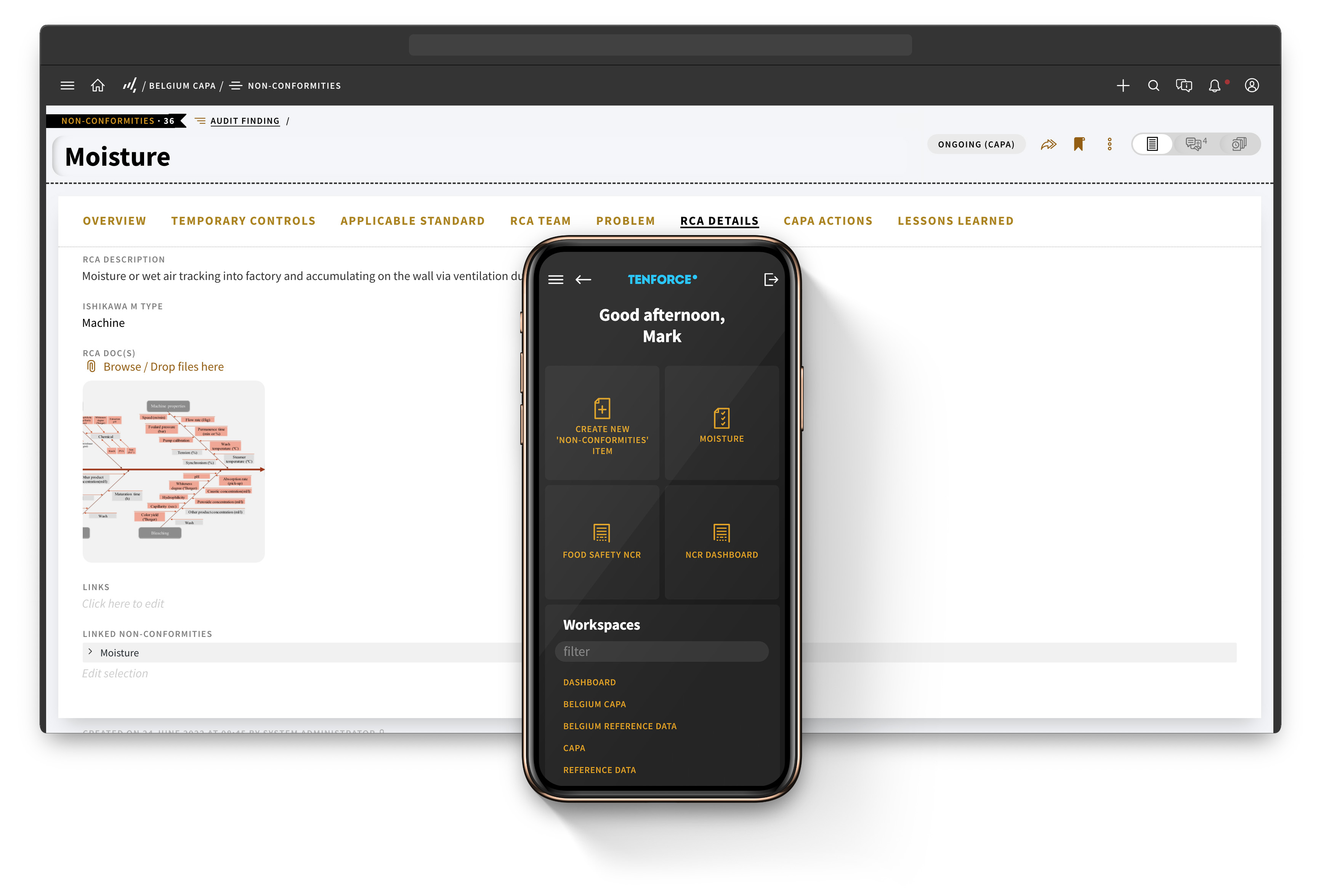
Centralize, automate, and follow through with your CAPA findings
Provide your team with a clear and easy-to-use process.
- Standardization of the CAPA process;
- Automated workflows and task management;
- Responsive and personalized interface for all users;
- Highly configurable platform to meet your specific CAPA requirements ;
- Ready to go in 8 weeks or less;
- Mobile ready; track CAPA progress anytime, anywhere;
- Evaluation of each step automatically built in;
- Fast, lean, and ready for the future.
Tenfore's specialists have a very good undertsanding of the industry. During the implementation of the Action Management module, we did an internal audit to establish the normal processes in our organization and then Tenforce took the lead and worked it out.
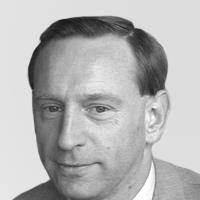
Get a clear overview of the status for all events
The Tenforce platform is highly accessible and easy to manage for all employees. You’ll get a clear overview of the controls in place and all the actions per non-conformity.
Retake full control of the CAPA process
The Tenforce Action Management module is built with flexibility in mind. It allows you and your team to have full control over the CAPA process for each department and site.
Move toward proactive work with predefined flows and clear steps
With root cause analysis built into the CAPA process, you can rest assured that future events and similar non-conformites can be avoided down the road.
Customer Stories
Using Technology to Streamline the CAPA Process Across the World
Discover how one of the world’s largest dairy companies ensures quality and safety from grass to glass across four continents.
The TenForce CAPA Management Process
Identify and Register Non-Conformities
- Determine risk category
- Event and risk categorize can be self-managed
- Events can be generated from other Tenforce modules, such as Audit Management
Describe the Problem
- A logical next step and necessary component for root cause analysis
- Links with other Tenforce modules when appropriate to automatically pull data
- Generates a small feedback loop to request more information and validate the information
Perform Root Cause Analysis
- Determine if a short-track RCA is sufficient or if a 6-stage RCA is more appropriate
- Select your root cause analysis team and methodology
- Upload additional documentation, media, and information
Define Your CAPA Action Plan
- Set up and determine your action plan before launching it
- Assign executors and resposible persons for each action
- Add more actions as the plan is put into place
Execute and Follow Up On Actions
- Maintain control of each step in the flow
- Manage non-conformity lifecycles
- Receive centralized control and automated reminders
Evaluate and Close
- Perform the “Check” phase of the Plan-Do-Check-Act cycle
- Evaluate each individual action for effectiveness
- Close actions with preliminary closure option available for final evaluations
Seamlessly integrate with other TenForce modules to unify your EHSQ processes
Audits & Inspections
Incident Management
LoTo
Permit to Work
Management of Change
Shift Management
Risk Management
Competence management
Quality management
Contractor Management
SAFETY DATASHEETS
MECHANICAL INTEGRITY
Document control
Complaint Handling
Environmental Management
CAPA
Environmental reporting
Compliance calendar
Dive deeper into this topic
Your peers trust us
Our customers rely on TenForce to foster a proactive safety culture and drive continuous process improvement. The outcome? Increased team efficiency, reduced administrative burden, and significant cost savings due to fewer fines and incident-related downtime.
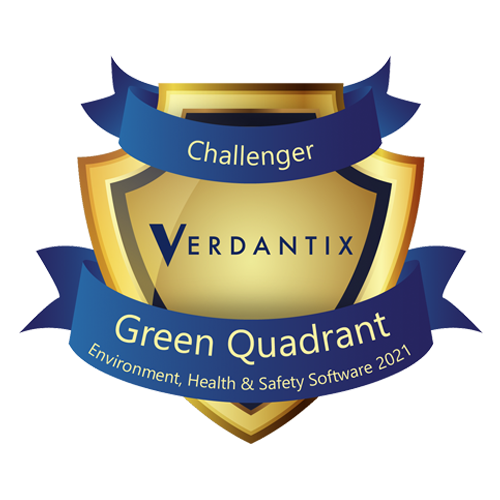
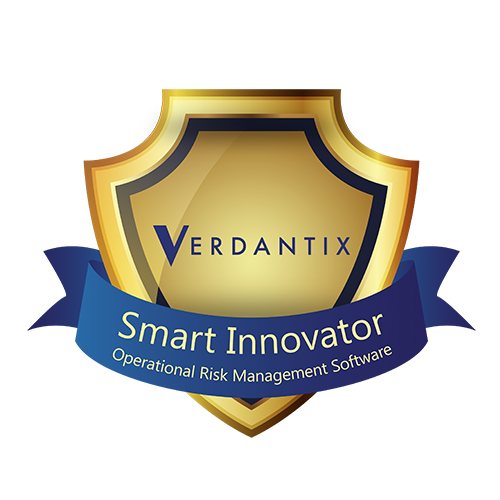
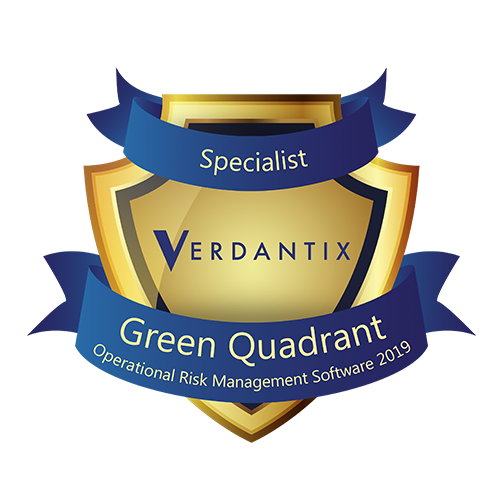
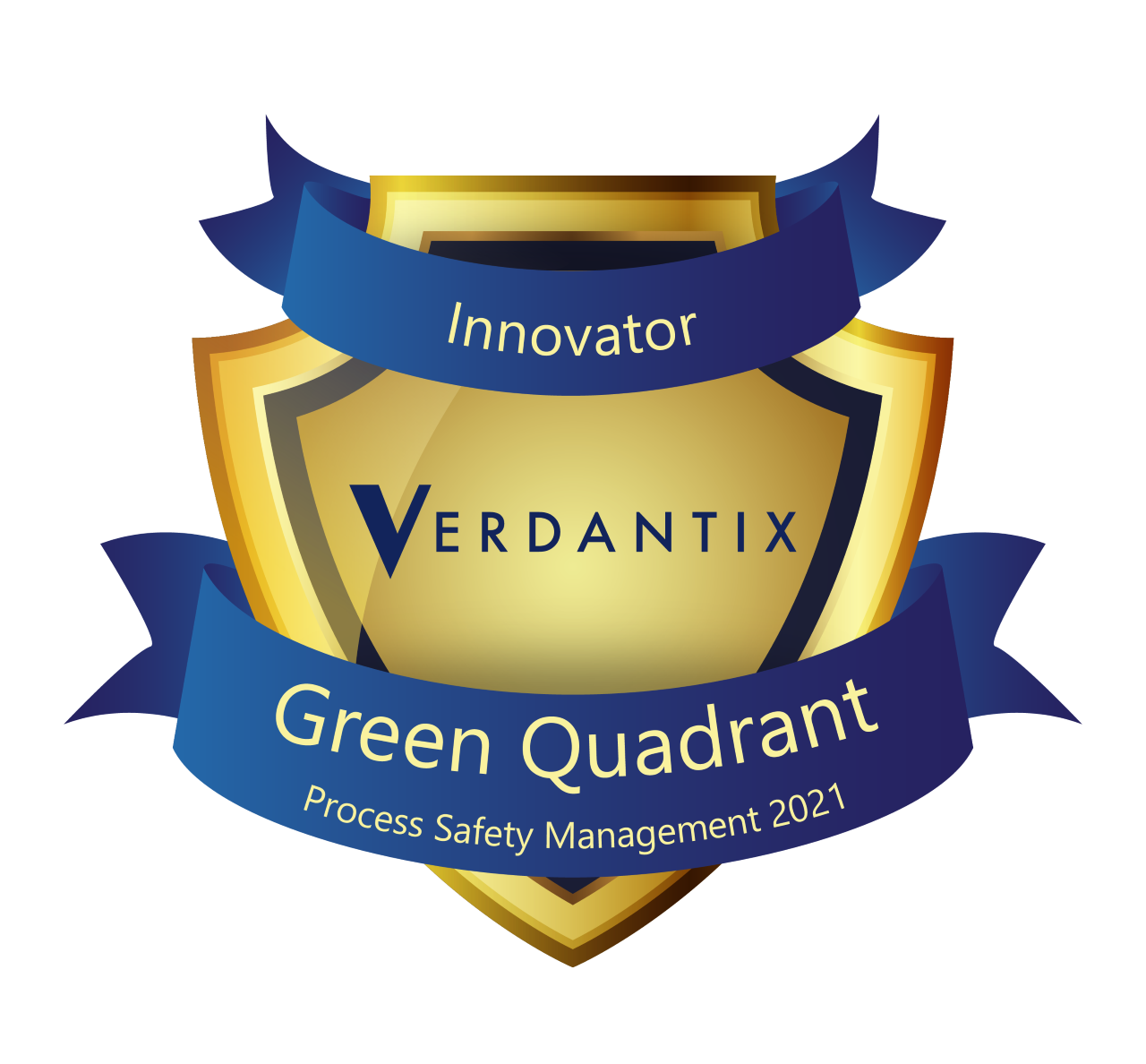
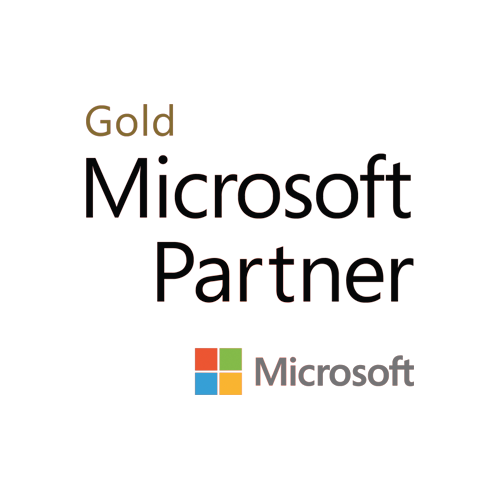
Book a demo
Curious to see how TenForce can make your workday easier? Book a demo, and we’ll show you what our EHSQ platform can do! One of our in-house experts will guide you through the ins and outs, showing you exactly how TenForce can tackle your challenges, whether it’s managing safety, streamlining compliance, or keeping quality in check.
So, choose a time that works for you, and let’s explore how TenForce fits into your day-to-day.
Ask us questions. Get clear answers. Share the recording with your colleagues.