Complaints spiraling out of control, or taking too long to resolve?
Swift Complaint Handling
Turn Complaints into Insights
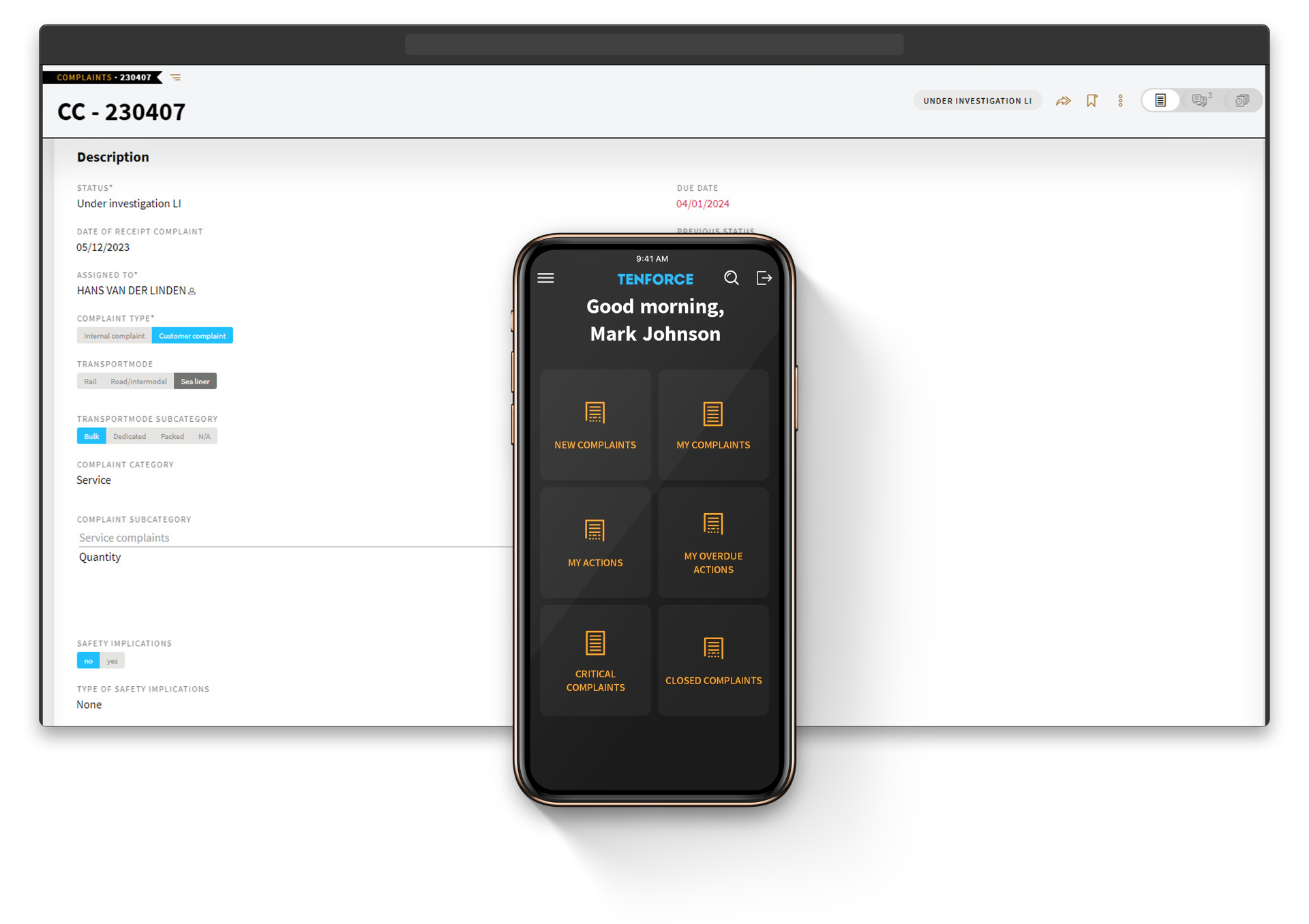
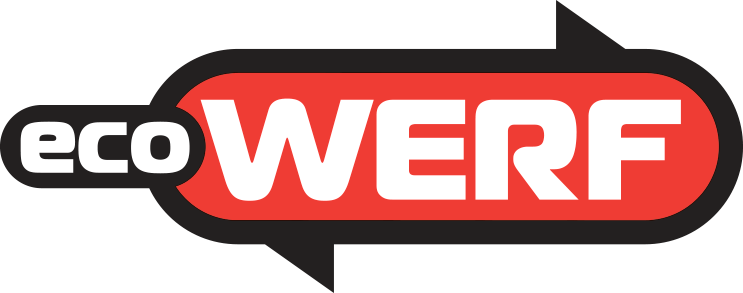
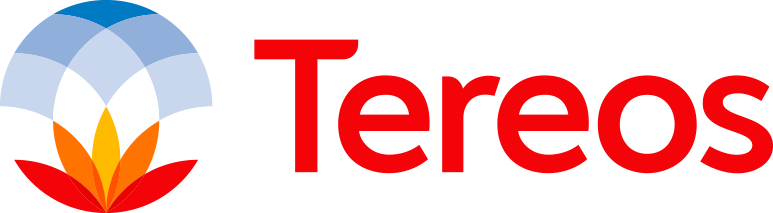
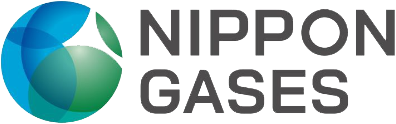
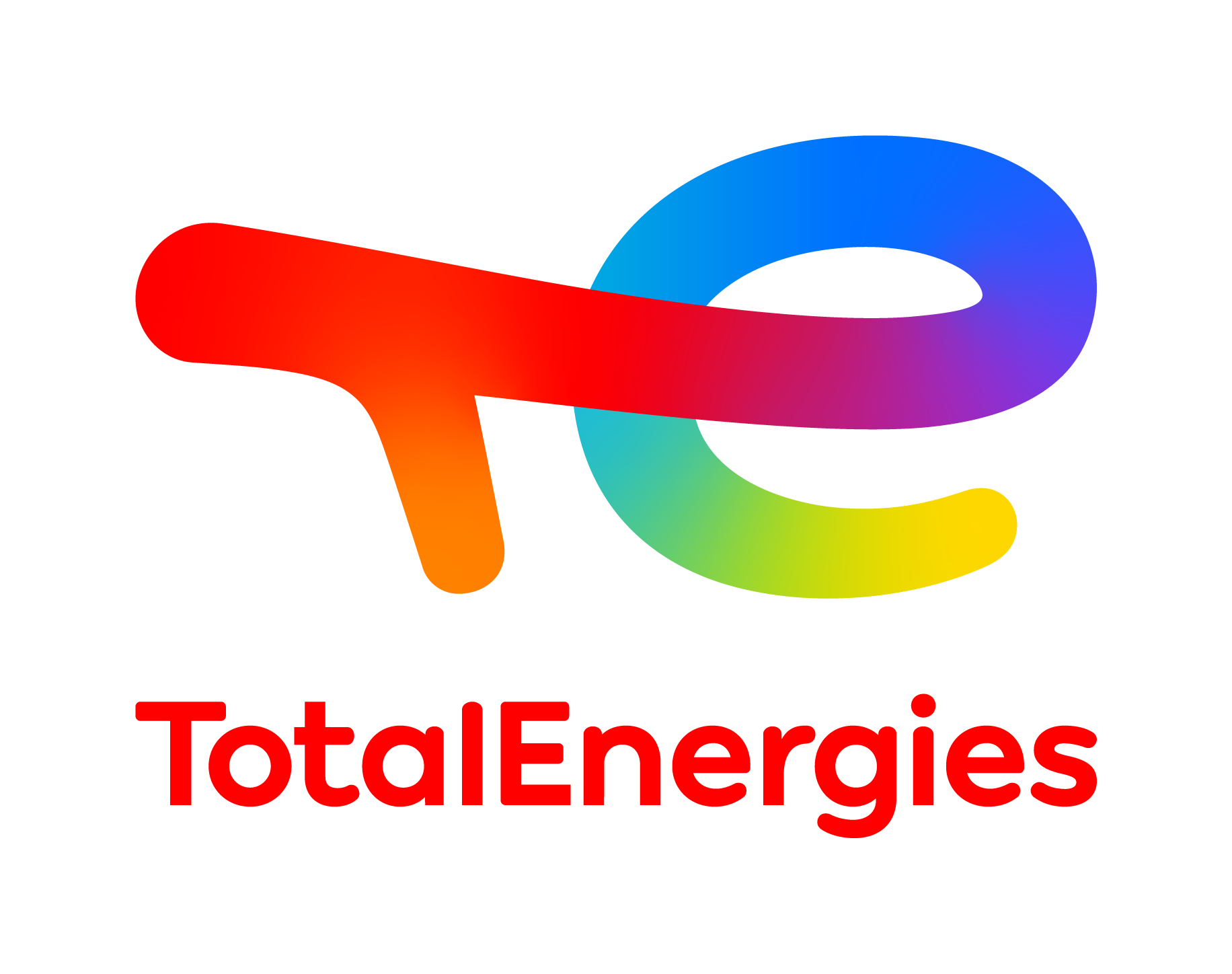
Address customer complaints swiftly with an end-to-end process
1
Plan
- Set clear objectives for resolving complaints
- Plan strategies to address various types of complaints
- Establish timelines and responsibilities for each step
2
Capture customer complaints
- Capture detailed information about each complaint
- Attach associated documents for record keeping and audit purposes
- Collect data from customers and suppliers from multiple sources (email, website form, etc.)
3
Take action
- Assign tasks and track progress in real time
- Categorize complaints by type and severity
- Connect complaints to nonconformance reports to generate corrective and preventive actions
4
Report and Analyze
- Generate customizable reports to track key metrics such as throughput, lead-times and number of open tickets
- Conduct in-depth analysis to identify recurring issues and patterns
- Gain valuable insights to optimize your complaint handling process
5
Close the loop
- Confirm that customer complaints have been resolved
- Ensure preventive measures are in place to mitigate future complaints
- Maintain compliance with industry regulations and standards
Grievances to growth: turning complaints into a competitive edge
Accelerate Complaint Resolution Times
Resolve complaints swiftly, with an automated process that keeps the right people in the loop with email notifications, automated task assignments, and reminders.
Drive Continuous Improvement with Root Cause Analysis
Consolidate complaint data to identify common issues and patterns quickly. Integrate with CAPA to accelerate action planning and manage improvement projects.
Ensure Compliance and Cost Efficiency
Avoid fines and regulatory repercussions by handling complaints efficiently. Cut down on Cost of Poor Quality (COPQ) by addressing complaints swiftly and thoroughly.
Enhance Brand Loyalty and Customer Delight
Spread the Voice of the Customer (VoC) across your organization by integrating with other modules. Build your brand reputation by transforming complaints into insights.
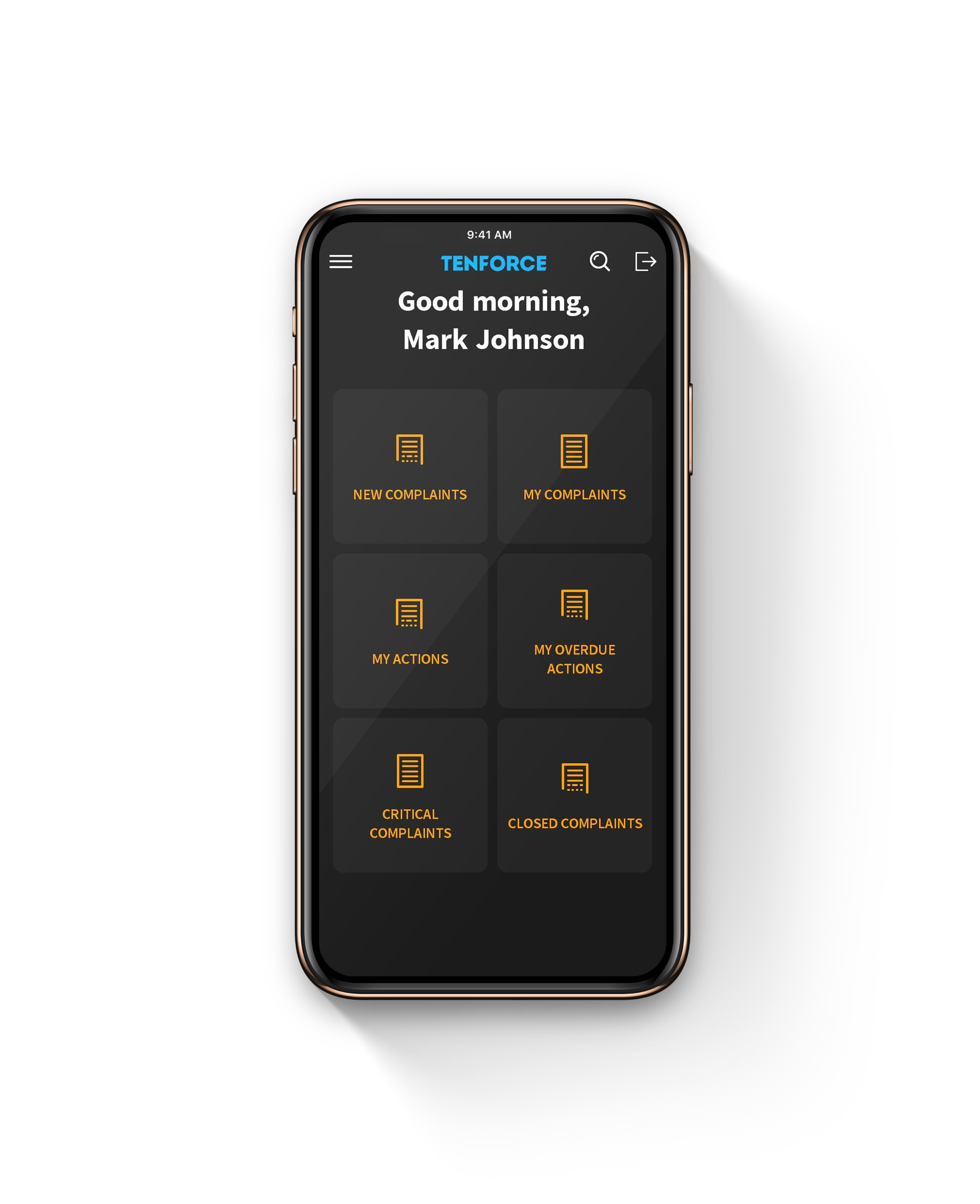
30%
faster complaint resolution
Seamlessly integrate with other TenForce modules to unify your EHSQ processes
Audits & Inspections
Incident Management
LoTo
Permit to Work
Management of Change
Shift Management
Risk Management
Competence management
Quality management
Contractor Management
SAFETY DATASHEETS
MECHANICAL INTEGRITY
Document control
Complaint Handling
Environmental Management
CAPA
Environmental reporting
Compliance calendar
Dive deeper into this topic
How TenForce Helps You Prove Compliance with Responsible Care®
Meeting Responsible Care® requirements isn’t just about following best practices—it’s about being able to prove that you do. That’s why the American Chemistry Council (ACC) requires members to implement a Responsible Care® management system and demonstrate compliance through documentation, audits, and continuous improvement.
TenForce makes this easier. Our unified EHSQ system brings everything together—so you can track safety measures, document environmental responsibility, and prove compliance with Responsible Care® at every step.…
TenForce & AIAS Supporting EHS Professionals in Italy
[EN translation below]
In TenForce, il nostro obiettivo è rendere il lavoro degli HSE più semplice e più efficiente—riducendo i rischi, semplificando la conformità e, soprattutto, facilitandoti la vita. Ecco perché siamo entusiasti di collaborare con AIAS, la principale associazione italiana per salute e sicurezza.
Chi è AIAS?Dal 1975, AIAS (Associazione Italiana Ambiente e Sicurezza) aiuta le aziende a creare una forte cultura della sicurezza. Connettono i professionisti EHS di tutta Italia, offrendo formazione, risorse e competenze tecniche su tematiche come la prevenzione dei rischi e la sostenibilità. …
What Chemical and Energy Leaders in Texas Can Teach Us About Zero-Incident Operations
Kuraray, Ascend, Kaneka, and Phillips 66—four chemical and energy giants operating in our Houston backyard. They manufacture everything from specialty chemicals to petroleum products, navigating hazardous materials, extreme temperatures, and heavy machinery daily. Yet, despite the risks, they share one goal: zero incidents.
How do they make safety second nature? Here’s what we can learn from the best in the chemicals, materials, and energy industries.
Keep talking about safetyToolbox talks, shift handovers, and pre-job safety meetings are great, but they’re not the only moments for safety discussions.…
How to Fit Safety Training into a Busy Schedule with Self-Paced Learning
Untrained employees, heavy machinery, and hazardous chemicals—it’s an accident waiting to happen. Knowing the risks and how to manage them is essential for the safety of everyone on-site, but training in busy workplaces isn’t always easy. Christophe Jacobs, Chief Customer Success Officer at FLOWSPARKS shares how digital, self-paced learning can improve safety for employees and contractors. And how, thanks to the integration of FLOWSPARKS with TenForce’s Competence Management, training is easy to create, follow, and track.…
Your peers trust us
Our customers rely on TenForce to foster a proactive safety culture and drive continuous process improvement. The outcome? Increased team efficiency, reduced administrative burden, and significant cost savings due to fewer fines and incident-related downtime.
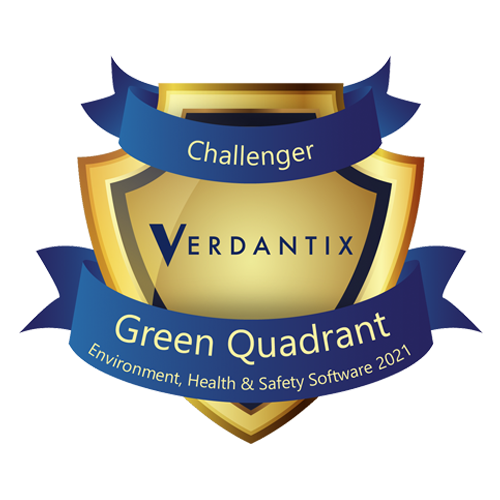
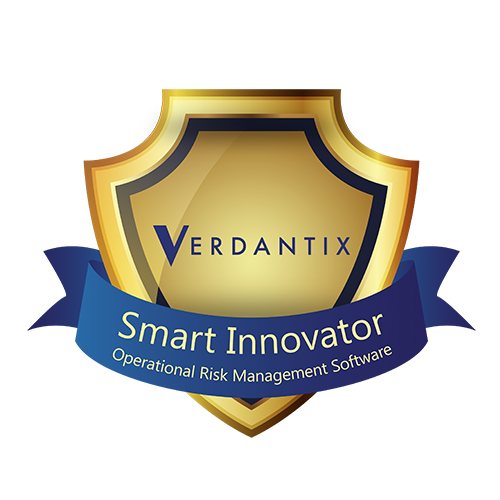
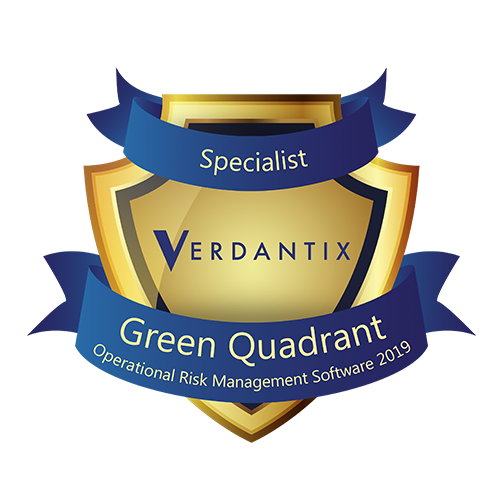
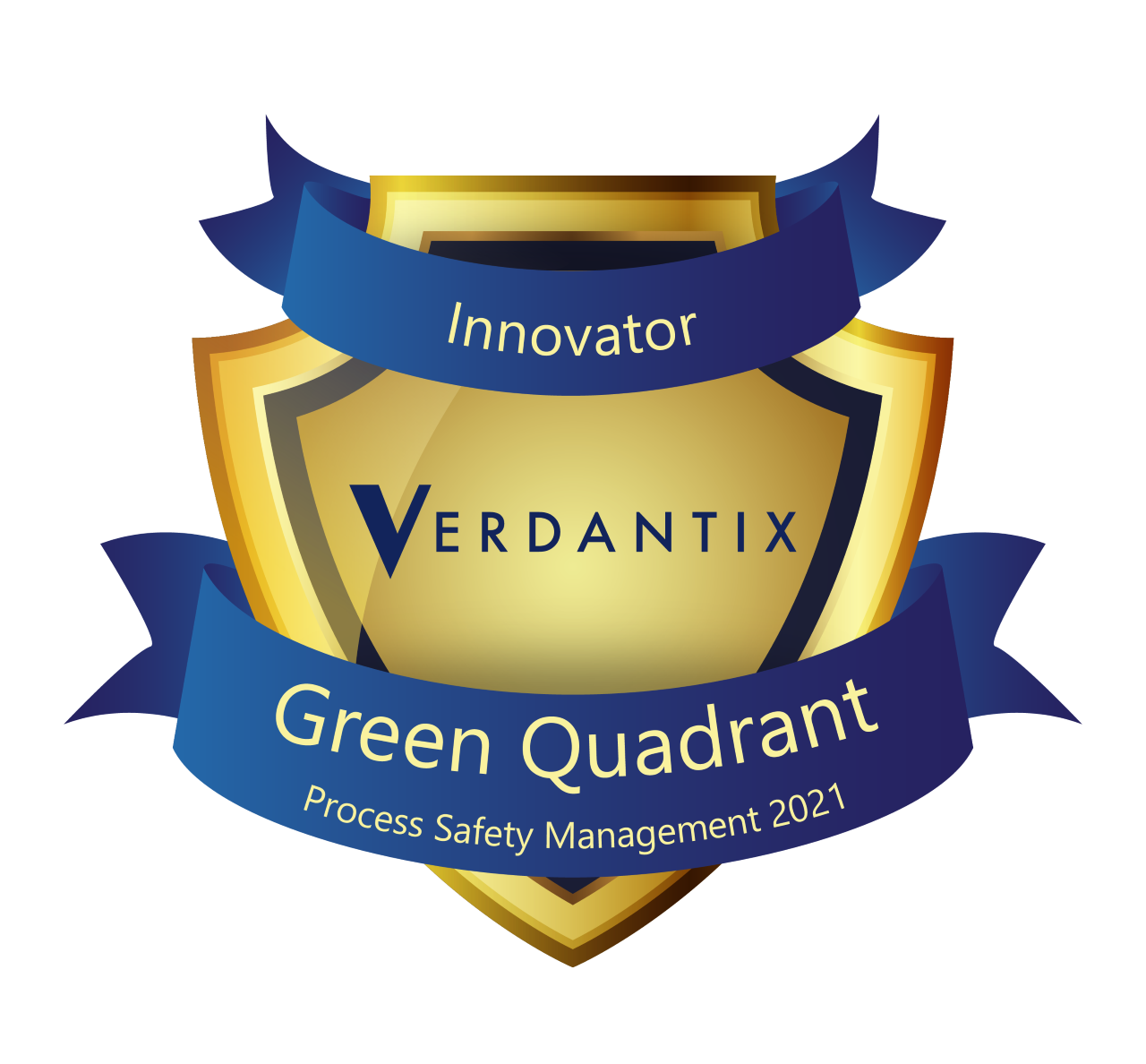
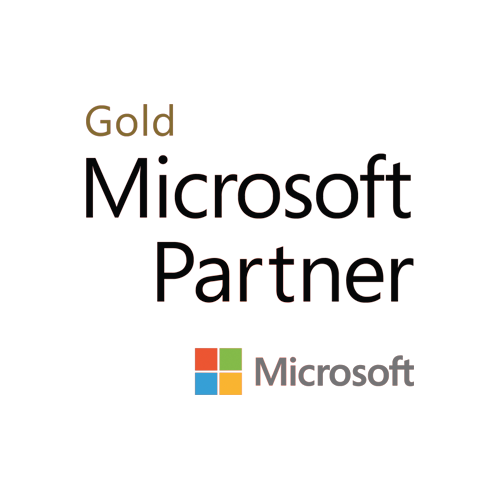
Book a demo
Curious to see how TenForce can make your workday easier? Book a demo, and we’ll show you what our EHSQ platform can do! One of our in-house experts will guide you through the ins and outs, showing you exactly how TenForce can tackle your challenges, whether it’s managing safety, streamlining compliance, or keeping quality in check.
So, choose a time that works for you, and let’s explore how TenForce fits into your day-to-day.
Ask us questions. Get clear answers. Share the recording with your colleagues.