Douglas Pharmaceuticals and TenForce Partner to Implement a Premier End-to-End Quality Management System
Douglas Pharmaceuticals, a leading New Zealand-based pharmaceutical company with over 700 employees, specializes in researching, developing, manufacturing, and distributing prescription, nutraceutical and over-the-counter drugs. With an annual manufacturing capacity exceeding 500 million tablets, they distribute to over 40 countries worldwide.
Product quality and patient safety are non-negotiable objectives for Douglas Pharmaceuticals. Aligned with their company-wide commitment to quality, they reflect the company’s dedication to upholding ethical principles.
Douglas identified an opportunity to build a Quality Management System (QMS) that would optimize its core processes and increase quality, without inflating costs. TenForce was approached as a partner for its functionality, user-friendly interface, and cost-effectiveness.
Through this partnership, Document Control, Corrective and Preventive Action (CAPA), and Management of Change (MoC) modules were reviewed, tailored and implemented.
Overcoming internal challenges
As part of a quality review, Douglas uncovered areas of improvement that would reduce the likelihood of errors occurring and provide consistency to the management of their processes.
Employee feedback also indicated that the previous system was time-consuming and causing frustration.
Implementing a comprehensive QMS to address these issues, which consolidated critical functions into a unified system, alongside considerations of cost, time, adoption, and platform integration, seemed daunting.
We’re challenging the outdated notion that quality must always come at a premium. Pharma must choose smarter, more cost-effective solutions to overcome cost pressures without compromising quality. TenForce offers a compliant solution at a lower cost than traditional pharmaceutical software providers. By implementing TenForce, we’re streamlining our operations and contributing to a better cost-benefit outcome.
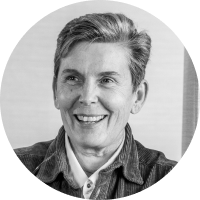
Building a unified quality management system, the lean way.
When it comes to reducing errors, a user-friendly system with streamlined workflows is essential. Managing various QMS processes without a relational database limits the ability to proactively identify trends, which over time, becomes costly.
With TenForce, Douglas sought to consolidate support for all QMS processes within a single platform. Moving from legacy management tools to a comprehensive relational database would enable easy data mining and trending, creating transparency of process flows while eliminating cumbersome manual administration:
The key to implementation success? Collaboration.
To improve project efficiency, Douglas managed the implementation of TenForce internally. Beatrijs Van Liedekerke, General Manager of Quality, brought her understanding of Douglas’ quality processes to the table, collaborating closely with TenForce to tailor the User Requirements Specification (URS) to their exact needs.
Through close collaboration, TenForce customized the Document Control module and implemented it in just three months, seamlessly migrating 6000 documents.
I don’t see TenForce as a supplier. I see TenForce as a partner. There is a willingness to collaborate, a willingness to expand, a willingness to listen and to work with us.
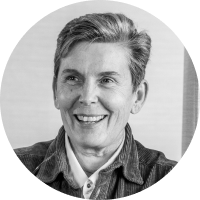
Choosing TenForce
The decision to choose TenForce was driven by three key factors:
#1 Straightforward user experience
TenForce stands out with its intuitive interface and effortless navigation, reducing the need for extensive training. Thanks to the straightforward user experience, learning all document management functionalities took only 2 hours of training. For more straightforward tasks like document lookup and read and acknowledge tasks, team members could rely on quick video tutorials (a few minutes long).
#2. Customization capabilities
Unlike their previous system, TenForce offered the flexibility to tailor the system to Douglas’ needs.
#3. Cost-effectiveness
With the pharmaceutical industry facing continuous cost pressures, there’s a great need to reduce the cost that comes with delivering quality. TenForce offered a cost-effective alternative to Douglas’ existing solution, making a greater number of modules available at a lower cost. By adding the CAPA and MoC modules on top of document management, Douglas now has an eQMS that supports their quality journey. Future additions of Audits, Complaints, and Quality Events modules will be added to the platform to complete the eQMS suite of applications.
There are good working instructions available, but after the initial training, people do not go back to them anymore because TenForce is so clear and intuitive, saving us a significant amount of time.
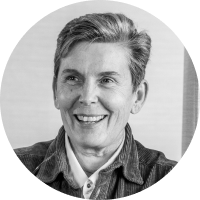
Time savings
TenForce has freed up 10% of the Quality Department’s time, boosting productivity by significantly reducing administrative tasks.
The solution is creating efficiency and transparency. It’s taking away the administrative burden and creating time to perform meaningful tasks to focus on quality.
Usability
TenForce’s document management search functionality lets users search within document content, not just their titles. As a feature that wasn’t available through their previous system, this has dramatically simplified document retrieval, benefiting the 70% of Douglas employees who use it daily.
Impressively, utilizing the CAPA module, 50 CAPAs were entered into the system within the first month of the CAPA module going live, without a single ticket or complaint.
The Douglas team loves it because it creates transparency and allows ease of navigation. They know it is facilitating their work.
Compliance
Using TenForce, Douglas has minimized the potential for human error, creating a more secure, audit-ready environment, reducing the risk of non-compliance.
Having TenForce in place limits the number of administrative mistakes. This immediately reduces non-compliance risks.
Douglas plans to roll out the remaining three modules – Audits, Quality Events, and Complaint Handling – by the end of 2024, solidifying their comprehensive QMS.
TenForce’s cost-effective, customizable, and compliant solution has streamlined Douglas Pharmaceuticals’ operations. As a QMS provider, they are a strategic choice for pharmaceutical companies looking to improve efficiency, quality, and compliance.
About Douglas
Douglas Pharmaceuticals is New Zealand's largest pharmaceutical company. They collaborate with innovative partners around the world to research and develop, manufacture, market and distribute prescription and over-the-counter pharmaceutical, nutraceutical and consumer healthcare products. Douglas is headquartered in Auckland, with an additional manufacturing site in Fiji.
Learn more at douglas.co.nz