5 Essential Steps to Strengthen Your Incident Management Program
From the moment materials enter your facility to when finished products leave the gates, risks are always present. These risks can harm your people, assets, and brand. That’s why an incident management program is crucial. It safeguards your workers and assets, ensuring a seamless flow from production to distribution.
In this blog post, we’ll walk you through the five key stages of an effective incident management program, share a top tip for success, and show how a digital solution can make all the difference.
What is incident management?
Incident management in manufacturing is all about keeping your workers safe and production running smoothly. It’s about spotting early signs, jumping into action, documenting what happened, analyzing the details, and correcting issues.
This process covers everything needed to handle disruptions smoothly, keep your workplace safe, reduce downtime, and boost productivity. It’s a comprehensive approach that makes your operations run like a well-oiled machine.
The 5 stages of incident management
Here are key steps for an effective incident management program:
#1. Plan and prepare
Here’s where you lay the groundwork for your strategy. First, identify the types of risks you face, and which are most common. Assess the probability of these risks occurring and determine their potential impact if they turn into incidents.
For example, you might find that chemical spills are your most frequent issue. Look at where these spills typically happen and consider the potential impact: a small spill might just need a quick cleanup and cause minor disruption, but a larger spill could mean significant downtime, health hazards for your team, and even regulatory fines.
Once you’ve identified and ranked your risks, it’s time to plan and prepare by considering:
- What measures can reduce the likelihood of risks materializing?
- What safeguards can be put in place to prevent incidents from happening?
- Are your workers equipped with the right tools and training to report incidents?
- How can you gauge the effectiveness of your measures and safeguards?
- How often will you review these benchmarks?
- How will you gather feedback on your strategies and tactics?
Answering these questions helps take your incident management program from reactive to proactive.
#2. Respond
Even with the best risk management, unexpected incidents can still happen. Whether it’s a minor disruption or a major crisis, your incident response should be swift and follow these steps:
- Immediately alert your response team
- Activate you pre-defined response protocols
- Send emergency alerts to inform and instruct all relevant parties
- Deploy your response team to the incident site
- Record incident details as they unfold or conduct a thorough debrief
- Once your response measures are completed, declare the incident over
#3. Document
Once the incident is contained it’s time to capture all the details. You can make this process flow more smoothly by:
- Gathering all details, including timelines, and involved equipment and personnel
- Compiling the data into a complete incident report
- Conducting a root cause analysis to figure out why the incident happened
- Evaluating how the incident affected staff and production
- Sharing lessons learned across the organization
By documenting and analyzing everything, your team can learn from the incident, improve safety protocols, and make your operation more resilient.
#4. Investigate
With the details documented, it’s time to dig in and uncover the truth. Scrutinize the evidence and analyze the data with these goals in mind:
- Identify the root cause of the incident
- Understand contributing factors
- Design measures to prevent recurrence
First responders may handle the immediate incident and submit a report, but it’s up to you to thoroughly examine incidents and find patterns that could signal broader issues. This will help you develop strong prevention tactics.
#5. Evaluate
Now it’s time to close the loop and critically review the incident management process to improve your response for the future. Here are the steps to take:
- Review how the incident was managed from start to finish to pinpoint strengths and weaknesses
- Scrutinize data and feedback to identify what’s missing and should be included next time
- Identify lessons learned and share this knowledge across the organization
- Update and refine policies to reflect the insights you’ve gained
These steps lay the groundwork for a strong manufacturing incident management program for your facility.
Our top tip
To stay focused when working through these five steps, keep these questions in mind:
- Has the incident happened before? When answering this question, you should decide what recurrence rate is acceptable.
- What was the impact? Here you should consider the direct and indirect cost per incident, and how the cost of incidents adds up over a year.
- Is the incident likely to happen again? You can estimate how likely recurrence is by looking through historical data and current conditions.
- What preventive measures are in place? This is where you need to critically assess the preventive measures you currently have in place.
- How can you further mitigate risk? If current measures aren’t enough, you should consider extra steps to reduce the likelihood or impact of recurrence.
Why you need a digital incident management tool
An effective incident management program relies on data – it helps you get to the root cause of incidents and implement the best preventive measures. That’s why a digital tool is essential. It streamlines the collection and collation process with:
- A user-friendly interface that makes it easy for workers to report incidents
- Pre-defined templates that ensure all the necessary details are collected, in a standardized way
- Customizable dashboards and reports that enable you to visualize data usefully for quicker and deeper insights
- Automated workflows and real-time alerts that ensure the right people are notified swiftly when an incident occurs
- Action management capabilities that help you launch investigations, assign tasks, and track progress
- Integrations with risk management and corrective and preventive actions to map the entire process, from assessing risks to mitigating them in the future.
See the 5 steps in action
Building a strong incident management program is key to keeping your manufacturing operations safe and efficient. By following these five steps—plan and prepare, respond, document, investigate, and evaluate—you can handle incidents better and prevent future ones.
Want to see how our digital Incident Management tool can help? Watch our expert-led demo to see TenForce in action.
Sign Up for email updates about our latest projects, articles and online events.
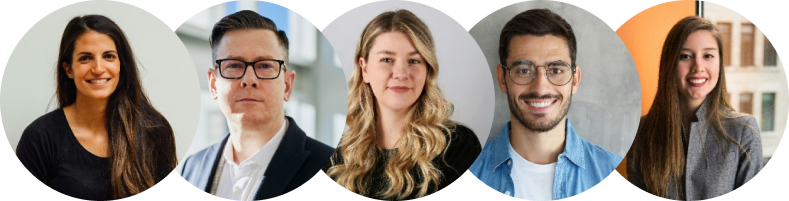