
INOVYN’s Digital-First Approach to Managing Change
Safety is the key priority for INOVYN, Europe's leading producer of vinyls. By focusing on both process and behavior safety, they create the secure environment for their employees, the production and the environment.
To avoid hazardous situations when implementing changes to their work processes, INOVYN uses TenForce Management of Change. Since embracing this fully digital approach to manage change, the transparency and efficiency of their process has increased.
Labor-intensive paperwork hinders efficient change
Before implementing TenForce, INOVYN had a different, homemade system in place to manage change. This way of working was limited: it could not expand or keep up to their evolving needs. The team had no choice but to operate according to the strict boundaries of the program.
This approach also didn’t eliminate cumbersome paperwork, which often led to multiple documents for the same job, but bearing different remarks. On top of this confusion, documents were also misplaced from time to time. Handling the administrative flow was almost a full-time job.
Efficiency and time were needlessly lost. INOVYN felt that it was time to look for a more flexible and transparent solution to manage installation changes.
A clear digital framework is a game-changer
Adopting and implementing a completely new system to manage change doesn’t happen overnight. To succeed, INOVYN communicated clearly with everyone who was going to be involved. By listening to every stakeholder’s needs, the willingness to embrace a new approach increased.
Soon after it’s integration, it was clear that TenForce Management of Change brings advantages for the whole company, from the engineering office to the management team.
TenForce means less paperwork, more transparency, and it’s clearer for everybody involved. The system is capable to keep up with our needs and is flexible enough to change when needed. The system works for us instead of the other way around.
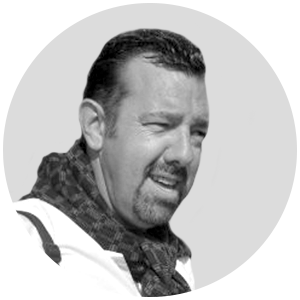
Bert Schietekat
The engineers benefit the most from the fully digital way of managing change. They need to know what changes are planned and have access to all the information to make the study. The core advantages for the engineering team are that TenForce is accessible to everyone and that all necessary data is available in the platform (ranging from P&IDs, schematics, budget related documents and info to actually signing forms).
Because of this transparency, the production team is also always aware when new changes in the process will be put in place. This way, they can prepare the necessary trainings and update their work procedures according to the upcoming changes.
For the management, the largest benefit is that they can easily follow-up with ongoing tasks and see the status of all the demands and studies. They can also export lists and data for reporting purposes.
What’s very useful for us is that you can track the history in TenForce of anything that happened. If someone has a problem, I can easily find out what happened. Another useful feature is the emailing and adding remarks. It’s not a general email that’s floating around but it’s linked to one particular part of the module, so everyone knows where to find it and look for it. This traceability is a big plus.
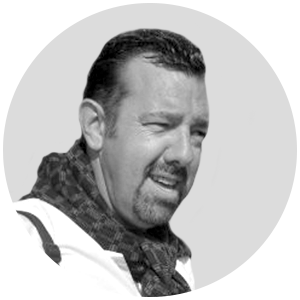
Bert Schietekat
Other departments are also included in the process, as changes to ICT, Lab, or the organization as a whole are also managed in TenForce MoC. Everyone works in the same way, with the same tools and according to the same guidelines. No matter which department is involved in the change, the process is accessible and clear for everyone.
Resilient software keeps up with unexpected change
INOVYN felt the impact of the COVID-19 pandemic on their regular way of working. As a production company, most staff members were still present on-site to do their jobs. However, management couldn’t always be physically in the office which could affect document flow.
COVID could have blocked our processes and could have caused delay on scheduled work since nobody was present on-site to sign off the documents that were already created in TenForce. The implementation of digital signatures made remote control and approval possible and assured that work was finished on time.
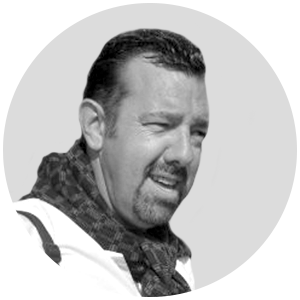
Bert Schietekat
Well-defined workflows in TenForce makes efficient management and approval of Management of Change documents possible even when people are working from home. Digital traceability is also assured. The need for everyone to be physically present was eliminated and the whole flow was digitized.
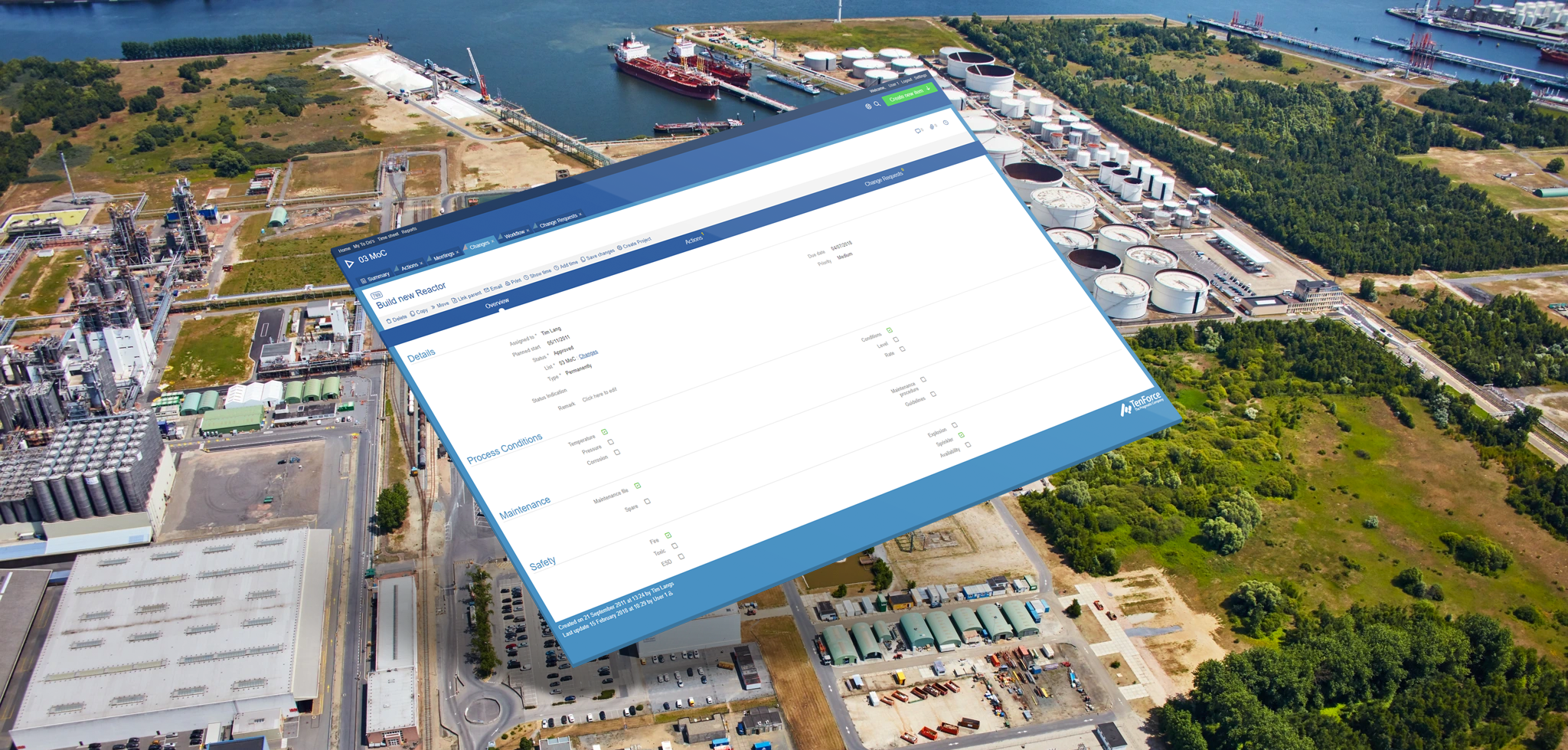
The results
Since 2008, INOVYN registered 1510 demands of changes in the TenForce MoC module. 1147 of these are executed. All info of these changes is available in the system and can be easily accessed at any time.
The speed and flexibility of the platform is one of the largest assets, especially now that installation changes are gaining momentum again after the slowdown caused by Covid-19.
During Covid, INOVYN employees could still progress critical safety tasks and approvals whether working on site or remotely. This enabled us to continue to introduce new installation changes with TenForce Management of Change thanks to the digital signatures we implemented.
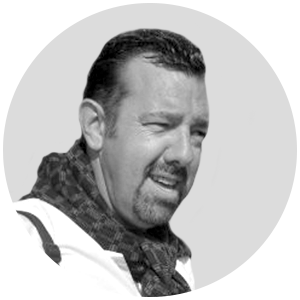
Bert Schietekat
With a solid system in place, INOVYN can continue to innovate and make changes to their installation. All this in a safe and efficient way, with a clear and transparent framework for everyone involved.
Get in touch with us
The TenForce team is here to help automate your EHSQ processes and help you transition from legacy systems to a modern EHSQ platform ready for real-time collaboration. Fill in the free trial request below to discover more about our software approach or book a consultation with one of our experts.
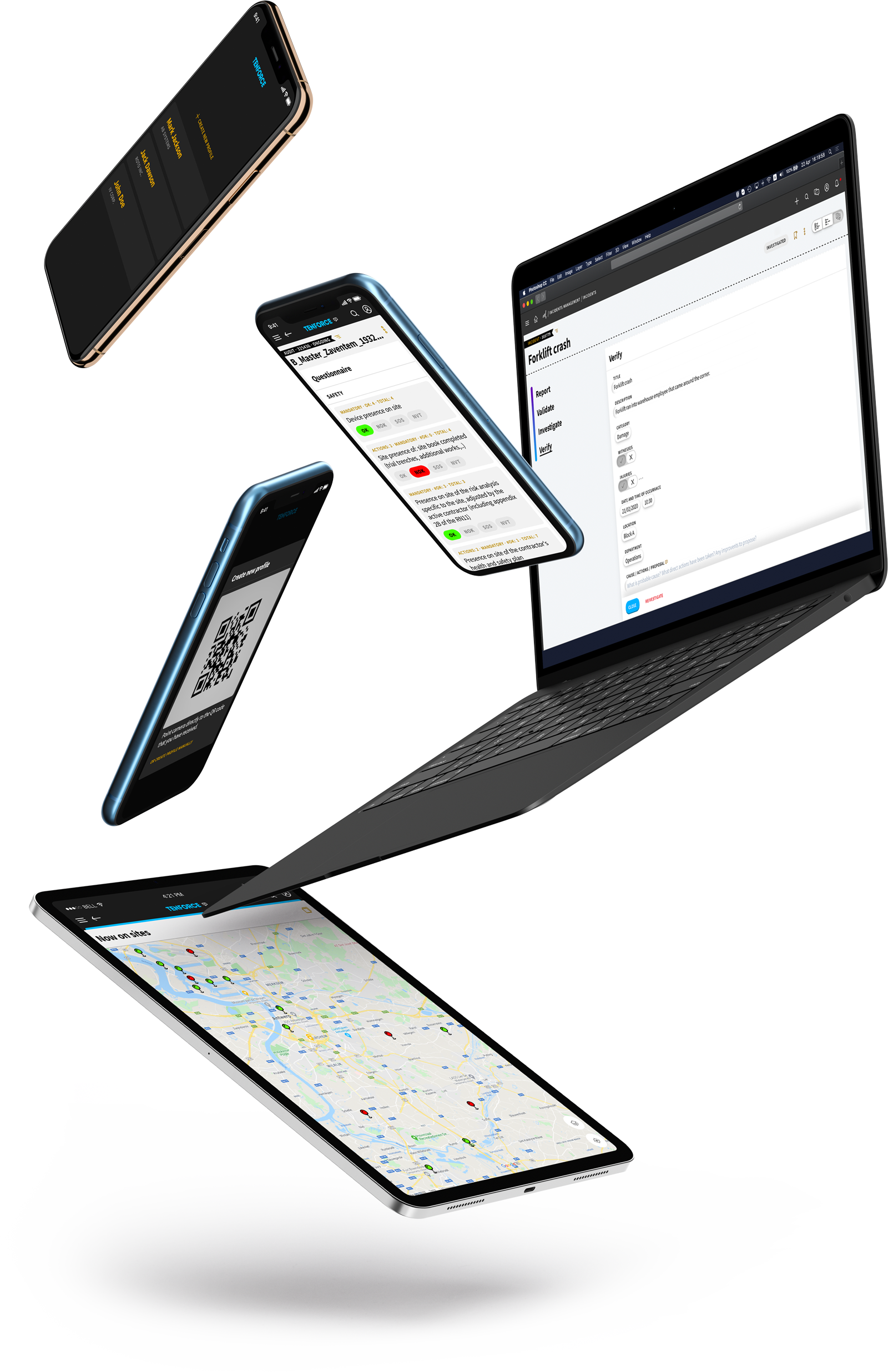